Introduction
In today’s high-pressure, resource-constrained business environment, lean team operations are becoming the norm. Whether due to budget constraints or strategic choice, Startups and SMEs — especially in manufacturing and operations-heavy sectors — must do more with less.
The good news? With the right systems, even a small team can function with the efficiency of a large, well-resourced operations.
Three critical pillars can help lean teams thrive:
- ✅ Standard Operating Procedures (SOPs)
- ⚙️ Workflow Automation
- 📊 Operational Visibility
Each element enhances efficiency and reduces dependence on specific individuals, paving the way for scalable and sustainable growth.
💡 We use MailerLite to power our lead magnets and client communications. It’s beginner-friendly, powerful, and highly affordable for SMEs
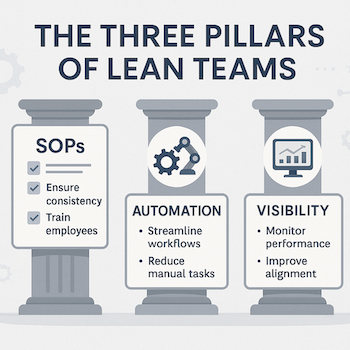
1. SOPs: The Backbone of Consistency and Clarity
Standard Operating Procedures are more than just dusty documents; they are the blueprint for operational consistency. In lean team operations, where multitasking is the norm and roles often overlap, SOPs help reduce ambiguity and ensure tasks are completed the right way, every single time.
Why SOPs matter:
- 🧩 Minimize human errors with clear, repeatable steps
- ⏱️ Speed up onboarding and training for new team members
- 📌 Promote accountability with defined responsibilities
Getting started:
- Keep it simple: Use checklists, flowcharts, or visual guides.
- Make them accessible: Store SOPs in a central, easy-to-navigate location like Notion or Google Drive.
- Review and revise regularly: Outdated SOPs can do more harm than good.
💡Pro Tip: Incorporate screenshots or videos or flowcharts into SOPs to improve clarity and make them more engaging for team members at all levels.
📈 Example: A startup in logistics implemented SOPs for its daily fleet dispatch. Within two months, new drivers were able to operate with 80% less supervision, and customer complaints dropped by 35%.
2. Automation: Multiply Your Team’s Productivity Without Hiring
Automation is no longer a luxury; it’s a necessity.
Repetitive tasks—follow-up emails, data entry, basic reporting—can and should be automated. This allows lean teams to focus on higher-value activities like customer engagement, problem-solving, and innovation.
Where to start with automation:
- Email Marketing: Use platforms like MailerLite to automate newsletters, onboarding sequences, and follow-ups.
- Task Management: Set up recurring tasks and reminders in tools like Trello or ClickUp.
- Data Reporting: Automate regular reporting using Google Sheets integrations or dashboard tools.
💡Pro Tip: Map out repetitive tasks performed weekly or monthly, and look for automation opportunities in just one process. The time saved adds up quickly.
📈 Example: A boutique manufacturing company integrated Google Sheets with WhatsApp API to send automatic daily production summaries to the management team. It saved over five man-hours per week.
3. Visibility: The Glue That Keeps Everything Aligned
Without operational visibility, even the best processes can fall apart. Lean team operations need real-time awareness of what’s happening across the board—production timelines, client deliverables, stock levels, and team capacity. Visibility enables proactive decision-making and prevents small issues from snowballing into major problems.
How to increase operational visibility:
- Use shared dashboards to track KPIs and progress.
- Hold quick daily or weekly check-ins to sync priorities.
- Adopt centralized tools for communication and documentation.
Visibility also supports transparency and collaboration. When everyone knows what’s going on, alignment improves, and unnecessary back-and-forth is reduced.
💡Pro Tip: Create a simple visual dashboard using tools like Google Data Studio or Monday.com to keep stakeholders updated at a glance.
📈 Example: An events company adopted a shared task board across departments to track venue readiness. The change improved deadline compliance by 50% and cut down internal email volume significantly.
Real-World Examples: Lean Team Operations Driving Big Results
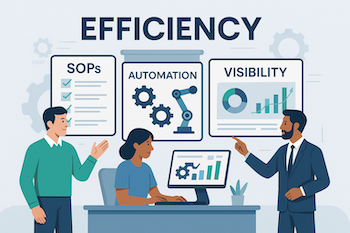
Lean principles are not theoretical—they deliver tangible, measurable ROI across industries. Leading organizations and research institutes have extensively documented how lean team operations boost efficiency, reduce waste, and drive profitability.
Case Study 1: Manufacturing SME
By implementing SOPs and automating order-to-dispatch workflows, a 5-person team cut manual reporting by 40% and reduced delivery times by 15%—in one quarter.
This mirrors what Toyota achieved through its renowned Toyota Production System, which emphasizes standardization, visual management, and continuous improvement (Kaizen). According to the Lean Enterprise Institute, Toyota’s approach reduced production lead time by over 90% and improved product quality—setting the global benchmark for lean manufacturing.
Case Study 2: F&B SME
After creating a simple visibility dashboard to monitor stock and prep, the team saw a 20% drop in food waste and a 30% boost in on-time deliveries within two months.
Similarly, Unilever implemented lean systems across its supply chain as part of its zero-waste-to-landfill initiative. According to a McKinsey & Company report, Unilever’s lean transformation helped improve overall equipment effectiveness (OEE) by 30%, while reducing operating costs and waste significantly.
More Industry Data:
A study published in the Harvard Business Review found that applying lean principles to knowledge work—like project management and service delivery—can boost productivity by up to 25%, simply by removing bottlenecks and clarifying ownership.
In fact, manufacturers that successfully implement lean systems typically enjoy 2–4% higher profit margins than their competitors, according to research cited by the Lean Enterprise Institute.
Conclusion: Lean Isn’t Less. It’s Smarter
Running lean team operations isn’t about cutting corners; it’s about maximizing impact with minimal resources. With the right SOPs, targeted automation, and shared visibility, lean team operations can achieve exceptional results.
These practices don’t require expensive software or external consultants—just a commitment to rethink the way work gets done collaboratively.
Call to Action:
Has your team embraced lean operations? What were the key enablers—or roadblocks? Share your experiences in the comments to help others on a similar journey.
💡 We use MailerLite to power our lead magnets and client communications. It’s beginner-friendly, powerful, and highly affordable for SMEs